AFRL’s Invent Program Tackles Aircraft System Efficiency
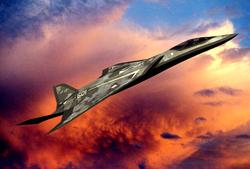
Credit: Lockheed martin concept
What began as a program to tackle heat issues on stealth fighters is evolving into the centerpiece of a U.S. initiative to address aircraft energy demands, and leading the drive toward engineering methods based on dynamic models. At the heart of the Energy Optimized Aircraft (EOA) national plan will...
Subscription Required
This content requires a subscription to one of the Aviation Week Intelligence Network (AWIN) bundles.
Schedule a demo today to find out how you can access this content and similar content related to your area of the global aviation industry.
Already an AWIN subscriber? Login
Did you know? Aviation Week has won top honors multiple times in the Jesse H. Neal National Business Journalism Awards, the business-to-business media equivalent of the Pulitzer Prizes.