Flight Tests Mark Key Stage For S-64 Composite Blade Program
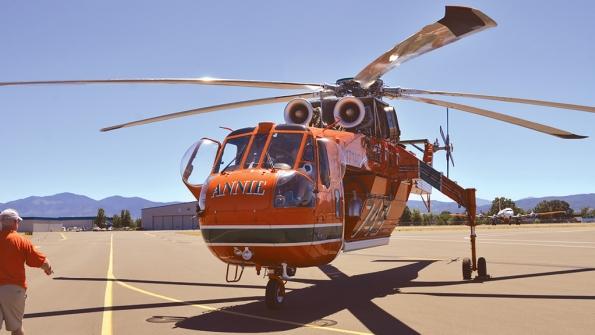
Credit: Erikson
Flight tests of Erickson Inc.’s long-running advanced composite main rotor blade upgrade for the Sikorsky S-65/CH-54 heavy-lift helicopter have accelerated, with completion now targeted by late summer and certification anticipated about six months later. The new blade is designed to significantly...
Subscription Required
This content requires a subscription to one of the Aviation Week Intelligence Network (AWIN) bundles.
Schedule a demo today to find out how you can access this content and similar content related to your area of the global aviation industry.
Already an AWIN subscriber? Login
Did you know? Aviation Week has won top honors multiple times in the Jesse H. Neal National Business Journalism Awards, the business-to-business media equivalent of the Pulitzer Prizes.