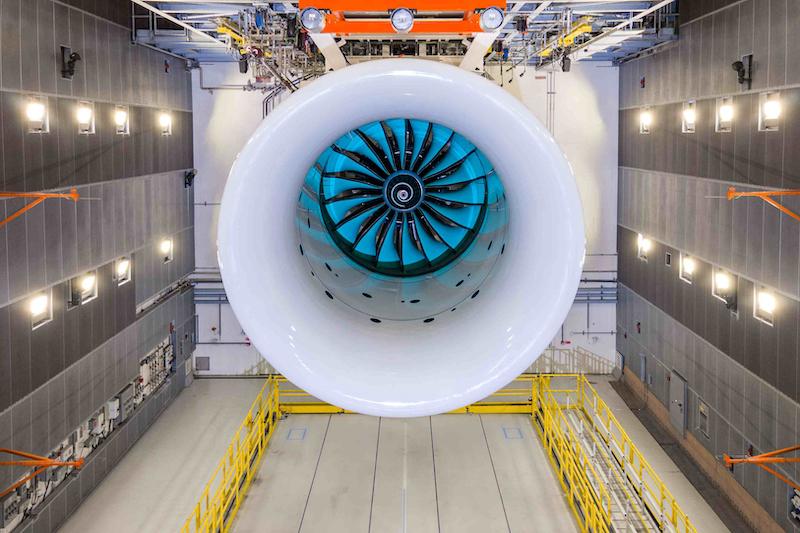
Rolls-Royce has run the UltraFan technology demonstrator at maximum thrust at its test facility in Derby, England, marking the highest power yet achieved by a gear-driven turbofan.
The engine, which first ran in April, achieved thrust of 85,000 lb. in early November, Rolls says. The power level is around 5,000 lb. higher than the target thrust level for which the demonstrator was designed.
Running in the company’s specially built Testbed 80 facility, the UltraFan is the first all-new centerline big-fan Rolls engine since the Trent XWB-84 in 2010 and comes nine years after the company revealed plans to pursue a geared architecture for its next-generation product line. Rolls adds that the initial stage of the test was conducted using 100% sustainable aviation fuel (SAF).
Although no new applications for the UltraFan have yet been identified, Rolls-Royce CEO Tufan Erginbilgic says the full-power milestone “puts us in a strong position to support the plans of our customers as they develop the next generation of super-efficient aircraft.” Technology from the program, including the widespread use of new materials, is also expected to be spun-off into upgrades of the company’s direct-drive engine family.
Simon Burr, Rolls-Royce group director of Engineering, Technology and Safety, says the UltraFan’s 10% efficiency gain over the company’s current production Trent XWB also underlines its strategy for more sustainable propulsion.
“We estimate that to reach Net Zero flying by 2050, a combination of highly efficient, latest-generation gas turbines such as UltraFan operating on 100% SAF are likely to contribute around 80% of the total solution, which is why today’s announcement is such an important milestone for Rolls-Royce and the wider industry,” Burr says.
Designed with a 140-in.-dia. fan—some 6-in. wider than the fan on General Electric’s GE9X, the largest turbofan currently flying—the UltraFan incorporates a 50-megawatt power gearbox developed at Rolls-Royce’s Dahlewitz, Germany facility. Other advances include a composite fan system, hybrid ceramic bearings, ceramic matrix composites (CMCs), high torque-density shafts, advanced cast bond turbine blades and second-generation nickel disk superalloys.
The CMC components, primarily used for turbine seal segments, are lighter and more tolerant of high temperatures. Made from a continuous silicon carbide fiber reinforcement with a fiber-matrix interface coating surrounded by a ceramic matrix primarily of silicon carbide, the CMCs and other high temperature features were previously evaluated in the HT3 (High Temperature Turbine Technology) demonstrator based on a Trent XWB-97.
Rolls says the UltraFan architecture is scaleable from 25,000-110,000-lb. architecture and, as part of more advanced studies under Europe’s Clean Aviation aeronautics research program, is involved in the HEAVEN (Hydrogen Engine Architecture Virtually Engineered Novelly) project. HEAVEN is a €35.6 million ($38 million) study aimed at scaling the concept to the short/medium-range market and integrating both hybrid-electric technology and direct hydrogen (H2) combustion.
The HEAVEN team includes academic, research and industrial partners across France, Germany, the Netherlands, Spain, and the UK, and will study an UltraFan H2 version with the goal of achieving a 20% fuel-burn reduction over current engines. HEAVEN is supported by Cavendish, another Clean Aviation program led by Rolls-Royce. Under the €29.2 million project, a design team will integrate lean-burn hydrogen combustion into a Pearl 15 donor engine for ground testing on liquid hydrogen starting in late 2024.