A Better Grease For High-Temperature Fasteners
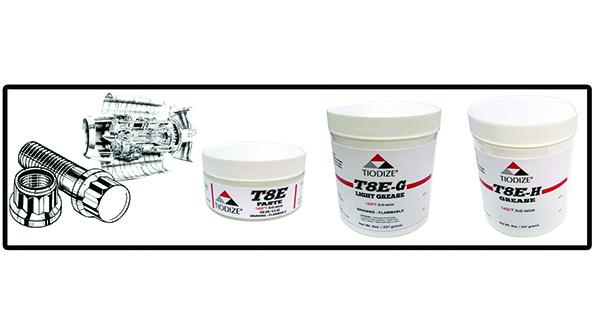
Credit: Tiodize
Tiodize has developed new greases that work at temperatures up to 1,400F. When applied to threaded fasteners in jet and other gas turbines, these new T8E greases prevent galling, or the cold-welding of two metals to each other. When galling occurs, parts must be cut apart or drilled out of a hole...
Subscription Required
This content requires a subscription to one of the Aviation Week Intelligence Network (AWIN) bundles.
Schedule a demo today to find out how you can access this content and similar content related to your area of the global aviation industry.
Already an AWIN subscriber? Login
Did you know? Aviation Week has won top honors multiple times in the Jesse H. Neal National Business Journalism Awards, the business-to-business media equivalent of the Pulitzer Prizes.