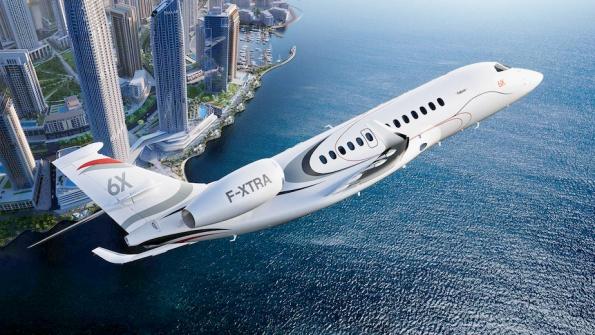
With advanced aerostructures technology already in flight test on an unidentified high-speed military aircraft and ground tests of new low-noise, compact nacelle concepts underway, UTC Aerospace Systems (UTAS) believes it is well positioned to penetrate the nascent civil supersonic market. The move...
Subscription Required
This content requires a subscription to one of the Aviation Week Intelligence Network (AWIN) bundles.
Schedule a demo today to find out how you can access this content and similar content related to your area of the global aviation industry.
Already an AWIN subscriber? Login
Did you know? Aviation Week has won top honors multiple times in the Jesse H. Neal National Business Journalism Awards, the business-to-business media equivalent of the Pulitzer Prizes.