Survey Finds Need For Better Tool Control
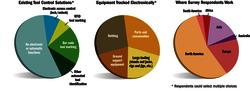
The aftermarket issued a no-confidence vote for its tool control practices—with one-quarter of respondents selecting “highest concern” in a recent Aviation Week survey. The Web-based poll, conducted in June and July, questioned the global civil aviation aftermarket industry about tool control...
Subscription Required
This content requires a subscription to one of the Aviation Week Intelligence Network (AWIN) bundles.
Schedule a demo today to find out how you can access this content and similar content related to your area of the global aviation industry.
Already an AWIN subscriber? Login
Did you know? Aviation Week has won top honors multiple times in the Jesse H. Neal National Business Journalism Awards, the business-to-business media equivalent of the Pulitzer Prizes.