SpaceShipTwo Debuts At Farnborough
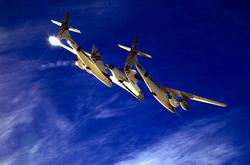
Credit: Mark Greenberg/Virgin Galactic
The Farnborough air show has seen plenty of “firsts” over the decades, but the appearance this year of the first passenger-carrying suborbital commercial spacecraft takes this prestigious event into new territory. The show debut of Virgin Galactic's SpaceShipTwo (SS2), albeit in full-scale replica...
Subscription Required
This content requires a subscription to one of the Aviation Week Intelligence Network (AWIN) bundles.
Schedule a demo today to find out how you can access this content and similar content related to your area of the global aviation industry.
Already an AWIN subscriber? Login
Did you know? Aviation Week has won top honors multiple times in the Jesse H. Neal National Business Journalism Awards, the business-to-business media equivalent of the Pulitzer Prizes.