Rolls’s Trent Family Upgrade Focuses On Fuel Burn
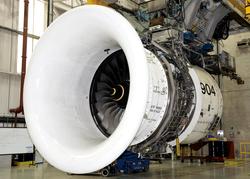
Credit: Rolls-Royce
As clearly indicated by the $4.7 billion in new widebody engine deals announced at the Paris air show, Rolls-Royce continues to bank heavily on the higher-value big-engine market. With around half of this newly signed business tied up in aftermarket support and sales of existing products, the...
Subscription Required
This content requires a subscription to one of the Aviation Week Intelligence Network (AWIN) bundles.
Schedule a demo today to find out how you can access this content and similar content related to your area of the global aviation industry.
Already an AWIN subscriber? Login
Did you know? Aviation Week has won top honors multiple times in the Jesse H. Neal National Business Journalism Awards, the business-to-business media equivalent of the Pulitzer Prizes.