Optimizing Maintenance Programs To Save Downtime
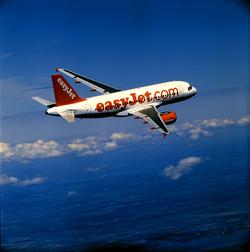
Credit: EasyJet
Most non-aviation people believe life's lone certainties are death and taxes. Those who understand aircraft operations know there is at least one more: maintenance downtime. Regardless of an aircraft's operating environment, configuration or utilization rate, being parked for maintenance always is...
Subscription Required
This content requires a subscription to one of the Aviation Week Intelligence Network (AWIN) bundles.
Schedule a demo today to find out how you can access this content and similar content related to your area of the global aviation industry.
Already an AWIN subscriber? Login
Did you know? Aviation Week has won top honors multiple times in the Jesse H. Neal National Business Journalism Awards, the business-to-business media equivalent of the Pulitzer Prizes.