Old And New Sensors Drive For High Resolution
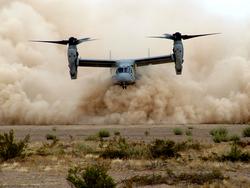
Credit: U.S. Air Force
Airborne intelligence, surveillance and reconnaissance (ISR) sensors continue to change rapidly, with much of that driven by operator needs. In particular, the level of detail required to track a suspect individual, identify a vehicle or find traces of a planted improvised explosive device (IED) is...
Subscription Required
This content requires a subscription to one of the Aviation Week Intelligence Network (AWIN) bundles.
Schedule a demo today to find out how you can access this content and similar content related to your area of the global aviation industry.
Already an AWIN subscriber? Login
Did you know? Aviation Week has won top honors multiple times in the Jesse H. Neal National Business Journalism Awards, the business-to-business media equivalent of the Pulitzer Prizes.