No Slowing Down As PT6 Marks 50th Anniversary
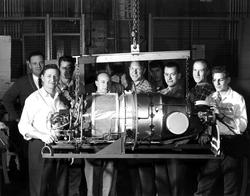
Credit: Pratt & Whitney Canada
On a chilly December day in 1963, when Pratt & Whitney Canada's turbine engine design group celebrated certification of their diminutive new PT6 turboprop, they had no idea they had given birth to one of the world's most successful propulsion concepts. Fifty years later, with more than 51,000...
Subscription Required
This content requires a subscription to one of the Aviation Week Intelligence Network (AWIN) bundles.
Schedule a demo today to find out how you can access this content and similar content related to your area of the global aviation industry.
Already an AWIN subscriber? Login
Did you know? Aviation Week has won top honors multiple times in the Jesse H. Neal National Business Journalism Awards, the business-to-business media equivalent of the Pulitzer Prizes.