NASA Focuses Supersonic Effort On Low-Boom Propulsion
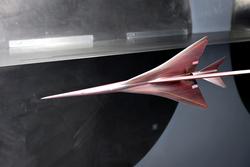
Credit: NASA/Lockheed Martin
The biggest barriers to development of economically viable and environmentally acceptable supersonic transports—sonic boom and airport noise—may be about to be breached. Through development of design tools allowing aircraft to be shaped to produce quieter booms, and noise-reducing nozzle concepts...
Subscription Required
This content requires a subscription to one of the Aviation Week Intelligence Network (AWIN) bundles.
Schedule a demo today to find out how you can access this content and similar content related to your area of the global aviation industry.
Already an AWIN subscriber? Login
Did you know? Aviation Week has won top honors multiple times in the Jesse H. Neal National Business Journalism Awards, the business-to-business media equivalent of the Pulitzer Prizes.