Honeywell Safety Aid Addresses Runway Excursions
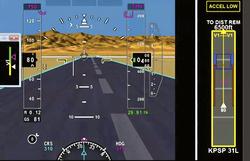
Credit: Honeywell
Honeywell is in hot pursuit of a new family of cockpit aids to help airline pilots better manage the takeoff and landing phases of their flights. The avionics maker is close to rolling out a takeoff-roll acceleration-monitor software upgrade as part of its enhanced ground proximity warning system...
Subscription Required
This content requires a subscription to one of the Aviation Week Intelligence Network (AWIN) bundles.
Schedule a demo today to find out how you can access this content and similar content related to your area of the global aviation industry.
Already an AWIN subscriber? Login
Did you know? Aviation Week has won top honors multiple times in the Jesse H. Neal National Business Journalism Awards, the business-to-business media equivalent of the Pulitzer Prizes.