Faster Finish
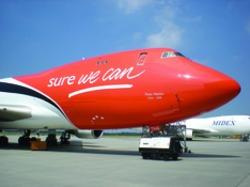
Credit: AkzoNobel Aerospace
The global economy and environmental concerns are changing the aircraft painting business as more MROs seek coatings with fewer hazardous materials and greater efficiency. “To reduce environmental and health risks, our customers are asking for primers and undercoats that are without chromates,” says...
Subscription Required
This content requires a subscription to one of the Aviation Week Intelligence Network (AWIN) bundles.
Schedule a demo today to find out how you can access this content and similar content related to your area of the global aviation industry.
Already an AWIN subscriber? Login
Did you know? Aviation Week has won top honors multiple times in the Jesse H. Neal National Business Journalism Awards, the business-to-business media equivalent of the Pulitzer Prizes.