Eclipse 550 Debuts
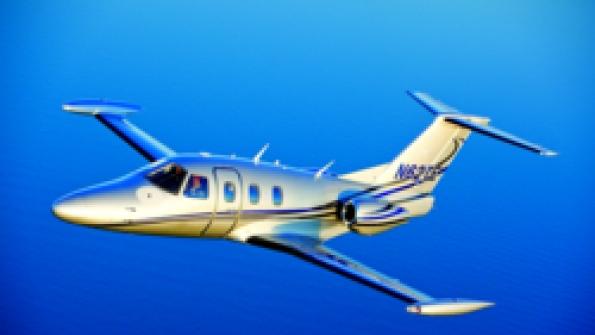
Plenty of diehard Eclipse 500 skeptics scoffed at Mason Holland, chairman and CEO of Eclipse Aerospace, when he announced at the 2011 NBAA Convention that his firm intended to resume building the aircraft sometime in 2013. Cynics all but buried the very light jet (VLJ) concept after EA500 production...
Subscription Required
This content requires a subscription to one of the Aviation Week Intelligence Network (AWIN) bundles.
Schedule a demo today to find out how you can access this content and similar content related to your area of the global aviation industry.
Already an AWIN subscriber? Login
Did you know? Aviation Week has won top honors multiple times in the Jesse H. Neal National Business Journalism Awards, the business-to-business media equivalent of the Pulitzer Prizes.