Composites, Metals Face Off For Next-Generation Single-Aisle
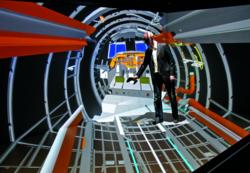
Credit: Dassault Systemes
The true test of whether composites can replace metals as the dominant raw materials from which aircraft are manufactured has still to come. Whether it is an all-new aircraft from Boeing before 2020 or Airbus after 2025, the next-generation single-aisle airliner will determine the balance of...
Subscription Required
This content requires a subscription to one of the Aviation Week Intelligence Network (AWIN) bundles.
Schedule a demo today to find out how you can access this content and similar content related to your area of the global aviation industry.
Already an AWIN subscriber? Login
Did you know? Aviation Week has won top honors multiple times in the Jesse H. Neal National Business Journalism Awards, the business-to-business media equivalent of the Pulitzer Prizes.