Boeing Switches To Repair Mode After 787 Fire
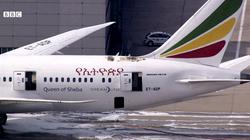
Credit: BBC NEWS
As investigations continue into the transmitter fire which severely damaged an Ethiopian Airlines 787 at London Heathrow Airport July 12, Boeing is gearing up for the most challenging aircraft repair and recovery operation it has yet faced on the new twinjet—and perhaps one of the most complex ever...
Subscription Required
This content requires a subscription to one of the Aviation Week Intelligence Network (AWIN) bundles.
Schedule a demo today to find out how you can access this content and similar content related to your area of the global aviation industry.
Already an AWIN subscriber? Login
Did you know? Aviation Week has won top honors multiple times in the Jesse H. Neal National Business Journalism Awards, the business-to-business media equivalent of the Pulitzer Prizes.