Avionics Integrity
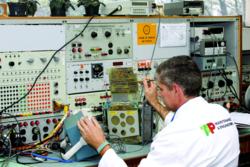
Credit: TAP Maintenance & Engineering
As airlines transition to a new generation of software-driven aircraft while continuing to fly older models with outdated electronics, industry concern is rising that avionics issues are a growing source of AOG (aircraft on ground) situations. “Avionics are among the top five contributors to AOG,”...
Subscription Required
This content requires a subscription to one of the Aviation Week Intelligence Network (AWIN) bundles.
Schedule a demo today to find out how you can access this content and similar content related to your area of the global aviation industry.
Already an AWIN subscriber? Login
Did you know? Aviation Week has won top honors multiple times in the Jesse H. Neal National Business Journalism Awards, the business-to-business media equivalent of the Pulitzer Prizes.