Avionics Giants Pursue Synthetic Vision For Credit
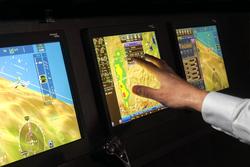
Credit: Rockwell Collins
Having gained a foothold in the flightdecks of high-end business jets, synthetic-vision displays are moving down-range to light jets and turboprops, and preparing to step across to the military arena. Eventually the commercial airline market will follow. Meanwhile, the ability to generate flight...
Subscription Required
This content requires a subscription to one of the Aviation Week Intelligence Network (AWIN) bundles.
Schedule a demo today to find out how you can access this content and similar content related to your area of the global aviation industry.
Already an AWIN subscriber? Login
Did you know? Aviation Week has won top honors multiple times in the Jesse H. Neal National Business Journalism Awards, the business-to-business media equivalent of the Pulitzer Prizes.