Tail Planning Enhances MRO Efficiency, Fleet Management
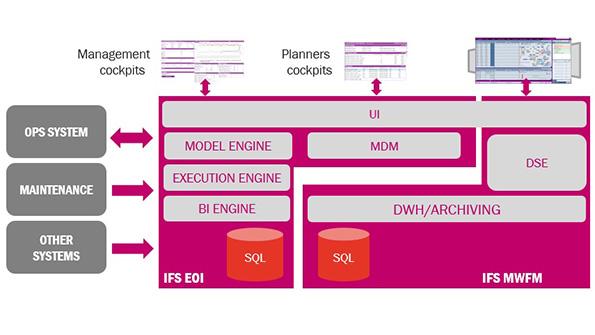
Credit: IFS
How do airlines optimize allocation of aircraft among routes, especially when they must react quickly to unexpected operational changes and unscheduled maintenance? Typical airlines dedicate a team for 3-4 hr. to optimize one day of flying, estimates Kevin Deal, vice president for aerospace and...
Subscription Required
This content requires a subscription to one of the Aviation Week Intelligence Network (AWIN) bundles.
Schedule a demo today to find out how you can access this content and similar content related to your area of the global aviation industry.
Already an AWIN subscriber? Login
Did you know? Aviation Week has won top honors multiple times in the Jesse H. Neal National Business Journalism Awards, the business-to-business media equivalent of the Pulitzer Prizes.