This article is published in Aviation Week & Space Technology and is free to read until Jun 01, 2024. If you want to read more articles from this publication, please click the link to subscribe.
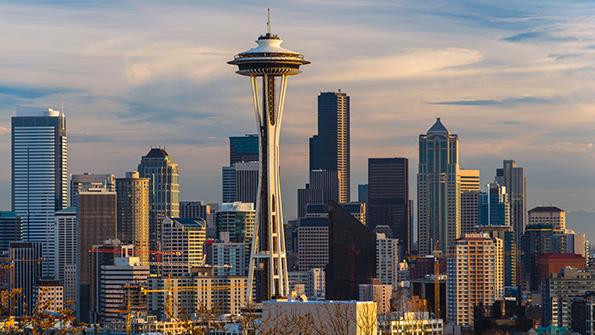
Boeing leaders made the “strategic” decision to separate themselves from aircraft production and development in Washington state in 2001. First, the corporate headquarters moved to Chicago. In 2022, it was moved again, to Arlington, Virginia, next to the Pentagon. The “New Boeing” was supposed to be a better way of operating. As then-Boeing CEO Harry Stonecipher explained in 2004: “When people say I changed the culture of Boeing, that was the intent, so that it’s run like a business rather than a great engineering firm.”
But two decades later, Boeing is neither a great business nor a great engineering firm. After two 737 MAX crashes in 2018 and 2019 killed hundreds of people and a MAX door plug blew out midair on an Alaska Airlines flight in January, the results are in. To secure its future, Boeing should return its headquarters to the West Coast—where a supermajority of aerospace innovation is being created—and specifically to Seattle, a city with the right mix of airliner development and production as well as the computing innovation needed to transform the company.
To claw back market share from Airbus and meet strict emissions regulations, Boeing needs to bet on bold innovation, including developing a commercial single-aisle airliner based on the NASA X-66A Sustainable Flight Demonstrator—a truss-braced wing design that promises 30% fuel savings when paired with a more efficient engine.
Boeing is shadowing the X-66A program with its advanced product development team and has lined up potential customers as a “sustainability coalition.” However, it needs to do more than flirt with the configuration—if flight testing confirms efficiency gains, the manufacturer must take the plunge.
Moving quickly from an X-plane to an FAA-certifiable commercial airliner manufactured at a high rate would be unprecedented. The X-66A would also be the biggest departure in the past 75 years from the tube-and-swept-wing design pioneered by the Boeing 367-80. Its thin, high-aspect-ratio truss-braced wing will require advances in composite manufacturing.
Designing and building a commercial version of the X-66A well and quickly would be the greatest engineering and innovation challenge Boeing has faced in decades. Trying to supervise that from 2,300 mi. away invites problems—a lesson the Boeing C-suite should have learned by now, especially after they missed dangerous assumptions underlying the 737 MAX’s Maneuvering Characteristics Augmentation System.
A new University of Pittsburgh study that analyzed tens of millions of research papers and patents found onsite teams had more breakthroughs than remote teams. Onsite teams are better at conceiving new ideas and designing new projects, the researchers hypothesize, because emerging concepts and knowledge can be hard to articulate, making it difficult to pass information to remote teammates.
Digital model-based systems engineering software promises to make the foggy ideas in engineers’ heads explicit to everyone. But Boeing’s digital engineering pathfinder effort with the U.S. Air Force T-7A Red Hawk shows how hard that is. Designed remotely by Saab in Sweden and assembled by Boeing in St. Louis, the T-7A was supposed to enter service this year. Instead, it is four years behind schedule and has racked up $1.33 billion in reach-forward losses.
Ironically, Boeing boasted that the T-7A would be easy to manufacture because it is made of metal. Building a commercial version of the X-66A would be far more complex, especially at production rates at least three times the volume of any composite airliner previously produced.
Boeing hopes to solve this problem by participating in NASA’s Hi-Rate Composite Aircraft Manufacturing project. If that delivers new composite thermoset and thermoplastic manufacturing and assembly technologies, transferring the knowledge to shop-floor machinists and suppliers will require close supervision.
To be sure, Boeing’s defense and space unit could remain in Virginia or return to St. Louis. But commercial aircraft are the company’s cash cow. In the Puget Sound area, Boeing leaders would be closer to the composites supply chain, including legacy suppliers like Toray Industries, as well as the innovative work of electric vertical-takeoff-and-landing aircraft developers in California that look to thermoplastic technologies to mass-produce air taxis. Seattle is also a world leader in software innovation, including artificial intelligence and cloud computing. Both are critical to enabling model-based systems engineering and new forms of generative engineering.
Boeing’s leaders could learn a lot from people in the West Coast’s software, advanced air mobility and space industries. The best CEOs in those sectors insist on working alongside their companies’ engineers and doggedly recite the mantra of “fail fast, learn faster.” Being a part of the innovation loop would be a big change from current Boeing senior leadership’s practice of “fail slow, learn slower,” in which problems are discovered only after aircraft have left the factory.
Comments